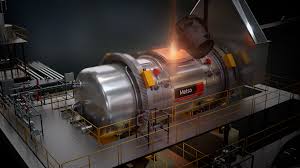
Lagos — Metso is launching a next-generation Anode Furnace for reducing CO2 emissions, improving impurity removal capabilities and bringing flexibility in treating secondary materials. The upgraded Anode Furnace is part of the Metso Plus offering.
“Raw materials pose both great challenges and opportunities for copper smelters today. Whether it is bringing in new primary concentrates, utilizing existing ones with degrading quality, or integrating secondary raw materials into existing processes, the demand for flexibility in the unit processes is growing. At the same time, the smelters are looking to identify potential reduction sources for greenhouse emissions, while the evolving raw material base is not making this paramount task easier,” says Miikka Marjakoski, Senior Sales Manager, Anode Casting and Anode Furnace Technologies at Metso.
“Metso’s Outotec® Anode Furnace is a great fit for solving these challenges. With its innovative CO2 emissions reduction solutions, improved impurity removal capabilities and the flexibility to treat secondary materials, it brings the long-trusted workhorse of the copper smelting industry into the modern era,” explains Marjakoski.
New features enable the reduction of CO2 emissions
The upgraded Anode Furnace features the latest design, advances in process safety, and ease of maintenance. Furthermore, it presents two exciting methods for reducing CO2 emissions.
“When it comes to CO2 emissions, the new Anode Furnace is unique. The process is fully prepared to utilize direct hydrogen reduction in the H2-ready variant. However, if the customer has no opportunity to switch to hydrogen use at present, Metso can also provide the technology to significantly increase the current gaseous hydrocarbon reductant efficiency with a steam-gas reduction system. Combining this with Oxyfuel combustion at the burners, the total reduction in CO2 emissions is demonstrably significant compared with traditional processes. This has also been proved through LCA calculations,” says Marjakoski.
The Anode Furnace delivery scope consists of all key equipment required for operating the furnace. Metso’s holistic competence in smelter process optimization and integration of automation systems ensures that the furnace will be seamlessly integrated into the processing chain in both brownfield and greenfield applications. When combined with services and on-site support, a smooth commissioning and start-up is ensured.
Furthermore, Metso’s Scrap Melting Furnace variant of the Anode Furnace presents an opportunity to treat a substantial amount secondary raw materials by utilizing integrated burners for melting purposes.
“The Outotec® Scrap Melting Furnace yields great flexibility in treating any mixture of molten copper from upstream processes and high-grade secondary copper feed directly into the anode furnace. It can be used as a stand-alone melting furnace utilizing solely secondary raw materials, making the product a go-to choice for primary and secondary smelters alike,” Marjakoski concludes.