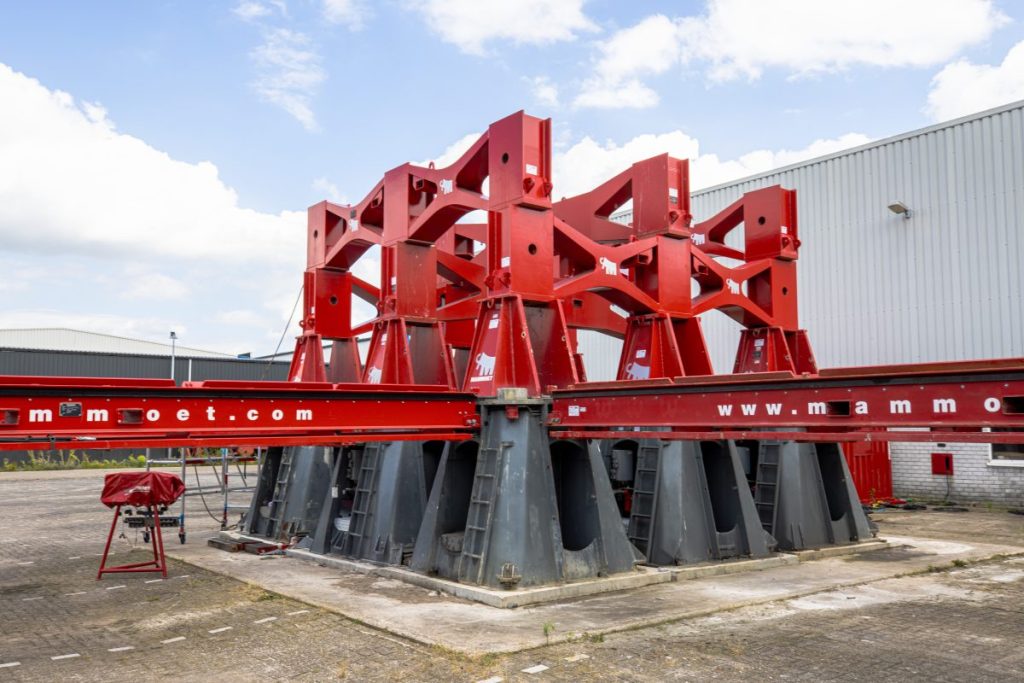
– Innovative new system reduces working at height and custom steelwork needs
Lagos — Mammoet has launched an increased capacity Mega Jack 10000, a new system that provides 10,400t of lifting capacity per tower – upgraded from 5,200t currently – without increasing the footprint of the tower base.
This means that less steel is required to support structures as they are lifted, and the heaviest lifts will be able to start meters closer to ground level.
Moreover, as the system’s capacity per tower has doubled, fewer towers will be needed to lift larger loads. This means smaller foundations are needed – further enhancing both scheduling and costs.
The Mega Jack 10000 introduces a revolutionary five-meter jacking beam with three connection points, allowing for load distribution across eight Mega Jack base units: four at the corners of the tower, and four at the center of each side.
Large jacking projects require starter beams, which are used to connect these jacking towers together and distribute the load. For example, if two Mega Jack 5200 towers are connected by a starter beam, they will be able to lift a load of 10,400t.
One Mega Jack 10000 tower can lift this weight on its own, meaning that lifts that would formerly require starter beams of two towers’ width may now only need one. So supporting steel can be smaller, thinner and require less engineering to develop.
This also reduces the lift’s starting height, making access easier and meaning smaller cranes are needed to complete projects.
Richard Verhoeff, Director Sales Global Special Devices at Mammoet, said:
“We noticed that loads were growing beyond the capacity of the Mega Jack 5200 and came up with the idea of the Mega Jack 10000. We designed an early initial concept and now we have upgraded the system to accommodate future projects that require a 10,000t single tower solution.
With the introduction of the Mega Jack 10000, Mammoet is setting a new standard in heavy lifting technology. This innovative solution not only increases lifting capacity but also enhances safety and sustainability by optimizing the jacking process.”
As part of the Mega Jack 10000 development program, Mammoet has also undertaken a root and branch upgrade of its control systems. Towers can now monitor lift positions to one hundredth of a millimeter, reducing stress on structures as they are lifted and so heightening levels of operational safety.
The new system will be utilized by the offshore oil and gas sector, for the manufacturing of heavy topsides, and the renewable energy industry for the fabricating of converter stations.
In these industry segments, loads can grow over 30,000t, and so require heavy lifting solutions that re-define construction methodologies to make them safer, more cost-effective, and efficient.